In a world where the construction industry generates over $9.5 trillion annually but has only seen marginal productivity improvements since the 1950s, innovation is crucial. While other industries have undergone digital revolutions and achieved remarkable efficiency gains, the construction industry has remained somewhat stagnant—until now.
From their headquarters in Denmark, Trackunit has spent 25 years bridging the gap between people and equipment. Today, they are a global leader, connecting more than 3 million construction machines and equipment, serving more than 5,000 customers, and harmonizing more than two billion data points daily across 120+ countries.
The core challenge was not a lack of data—Trackunit had already created one of the world's most extensive data lakes for construction machinery. The challenge was to humanize this vast amount of data: to transform cold numbers and graphs into meaningful insights and actionable steps. Even though machines generated billions of data points, years of experience were still required to interpret and act upon this information. No two job sites are the same, thousands of different machine types operate under varying conditions, and a lack of industry-wide standardization makes data interpretation even more complex.
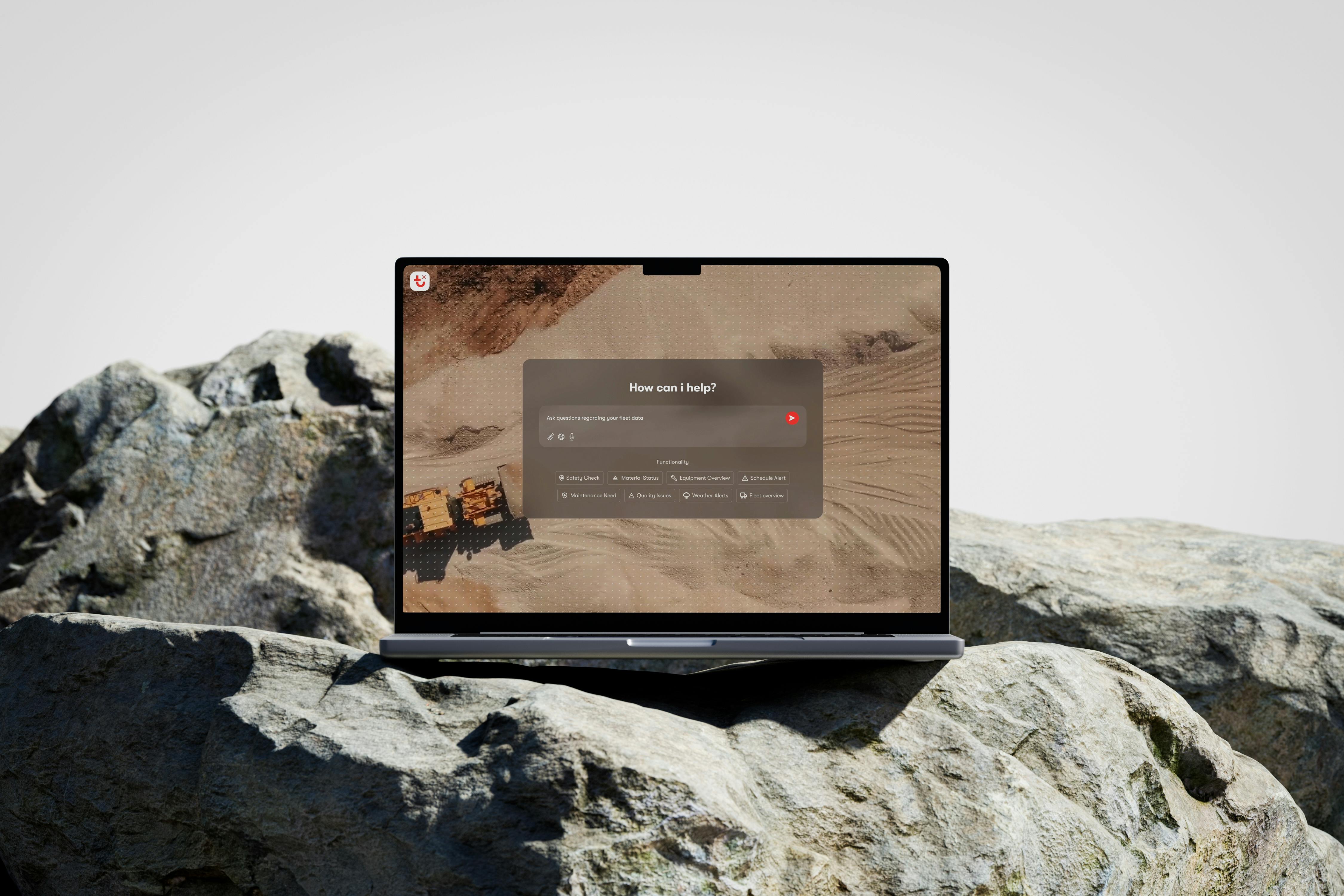
Trackunit's innovation demonstrates the power of letting machines communicate their needs through data. By creating an AI system that "speaks machine," they've transformed what was once just raw data into valuable insights that predict maintenance needs, optimize fleet placement, and accelerate thousands of daily decisions.
By presenting complex insights in a humanly understandable manner, Trackunit Luna has democratized access to advanced data analytics. This allows a broad range of users—not just data scientists or engineers—to make better, faster decisions, bridging the growing skills gap in the construction industry.
Trackunit's story highlights how AI can simultaneously drive operational efficiency and sustainability. Through better fleet utilization and reduced downtime, companies can maximize their existing resources, reducing the need for additional equipment and the associated environmental impact. This efficiency-first approach creates both economic and environmental benefits across the value chain.